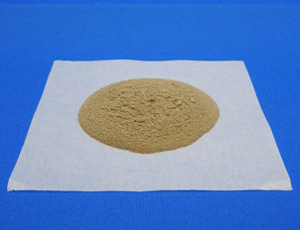
今回開発した表面ポリオール還元法で作製したディーゼル酸化触媒(提供:産業技術総合研究所)
(独)産業技術総合研究所と(独)新エネルギー・産業技術総合開発機構(NEDO)は7月3日、ディーゼルエンジンの排ガスを浄化する触媒の新製法を開発したと発表した。これは、現在の製法より白金など白金族元素の使用量を50%も減らす一方で、現用品と同等以上の炭化水素浄化性能を持つ触媒を製造できる製法。
■耐熱性向上、量産性も
白金族元素は、白金やパラジウム、イリジウムなど6種類の元素のこと。中でも白金は、工業分野に幅広く使われ、特に多いのが自動車排ガス浄化触媒への利用で、白金需要の半分近くを占めている。このため、今後の新興各国の自動車排ガス規制の強化や世界的な自動車需要の増加見通しから、白金の供給不安が懸念され、ディーゼル酸化触媒の白金使用量低減が喫緊の課題になっている。そこでディーゼル酸化触媒の新製法をNEDOのプロジェクトとして2009年度から5年間かけて産総研が開発を進めてきた。
ディーゼル酸化触媒は、高温に曝され、触媒の白金粒子が熱によって劣化する。その熱劣化を補うのに多量の白金が使われ、白金粒子の耐熱性向上が白金使用量低減の鍵とみられている。
産総研は、白金とパラジウムを複合化した大きさ(粒子径)がナノメートル(nm:1nmは10億分の1m)オーダーのナノ粒子触媒が耐熱性の向上に有効であることを見つけ、「白金‐パラジウムナノ粒子触媒」を大量製造する方法を開発したもの。
新製法は、「表面ポリオール還元法」といい、ポリオール(多価アルコール)に白金とパラジウムの両化合物(貴金属塩)を溶かし、それを担体と呼ばれるアルミナの粉末に浸み込ませ、窒素気流中で加熱し、担体の表面上に粒子径が3nm程度の白金ナノ粒子を析出させるという方法。
産総研は、今後、量産試験や触媒の実車評価を行い実用化につなげていく計画。