(独)産業技術総合研究所(産総研)は3月10日、新東工業(株)、新東ブイセラックス(株)と共同で遠心力による均一加圧を利用した新プロセス「遠心加圧溶融法」を開発、厚さ数百µm(マイクロメートル、1µmは100万分の1m)の単結晶に近いビスマス・テルル系高性能熱電厚膜を作製することに成功したと発表した。 導体の両端に温度差をつけると、温度差に比例した電位差(電圧)が生じる熱電素子は、熱エネルギーを直接電気エネルギーに変換でき、[1]可動部分がないため信頼性が高く、メンテナンスフリーで長寿命、[2]小規模でも効率が低下しないなどの特徴があり、工場や自動車などから発生する未利用の廃熱を電力に変換して有効利用できる。 しかし、民生・産業用として使用するには、エネルギー変換効率が低く、発電素子の製造コストが高いことから、一部の特殊な例を除き採用されなかった。 産総研など3者は、遠心焼結技術とその関連技術を、熱電厚膜作製に応用し、高出力化、低コスト化、小型化を目指した共同研究に取り組んできた。 熱電厚膜は、主にスクリーン印刷焼結法やメッキ法によって作製されているが、新技術はあらかじめ溝加工を施した型(絶縁酸化物の基板)に原料粉末を所定量充填し、閉鎖空間で基板の厚さ方向に遠心力を加えながら、原料を溶融・凝固させて熱電厚膜を得る方法。非接触の均一加圧により密度がほぼ100%の膜が得られる。 メッキ法では、厚さ数百µmの厚膜の作製は困難だが、新製法は厚さ数十µmから数mmまでの厚膜の成膜が可能という。 高性能厚膜熱電素子の作製法が開発できたことから、「今後は実用可能な熱電素子の開発を進め、早急に廃熱エネルギーの有効利用を実現させたい」と産総研ではいっている。 詳しくはこちら | 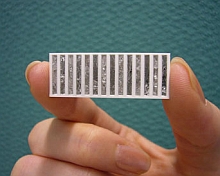 |
新製法を使って作ったビスマス・テルル系厚膜熱電素子(提供:産業技術総合研究所) |
|